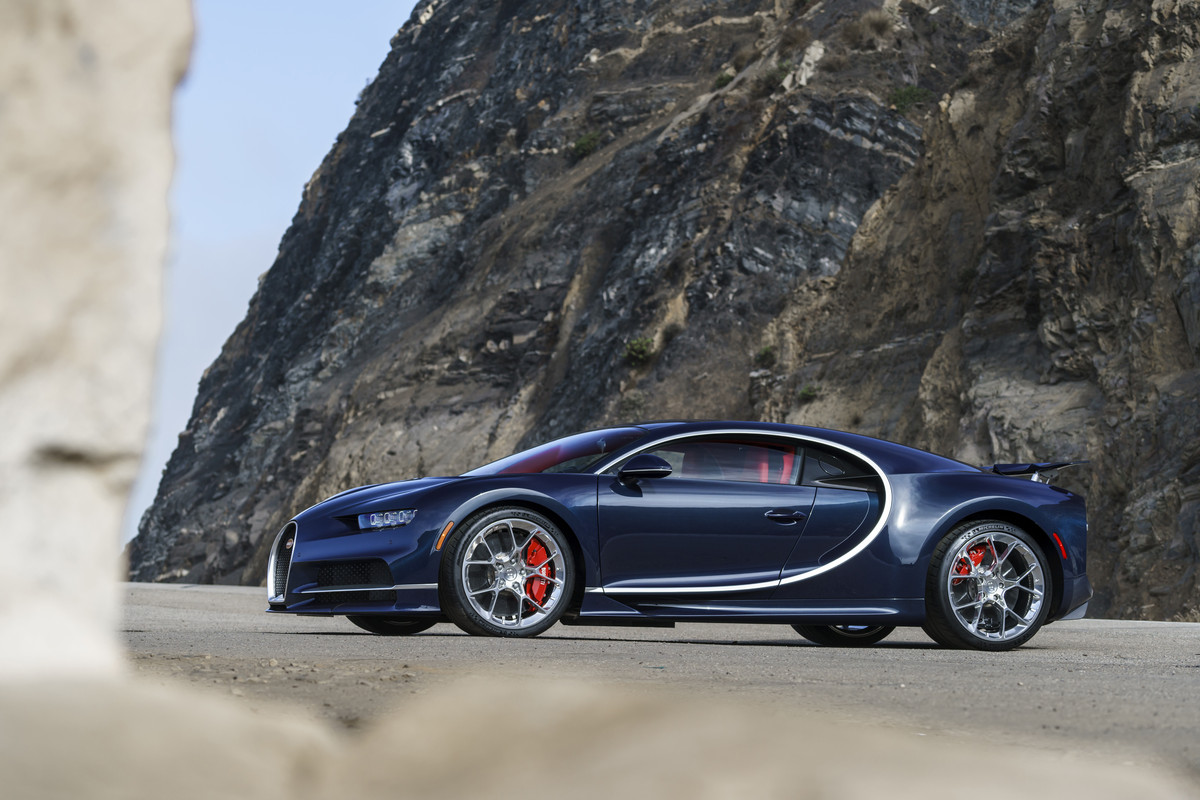
Bugatti fabrique les futurs étriers de frein de la Chiron en impressions 3D.
On le sait, chez Bugatti tout est extrême. La puissance des moteurs est phénoménale, les performances sont stratosphériques et les matériaux utilisés sont précieux… C’est quand même le minimum syndical pour une voiture facturée au bas mot, 1 300 000 € (Veyron 2013). Mais au-delà du produit fini, ce sont les moyens de développement et le mode de fabrication qui sont tout aussi extrêmes. Preuve en est, les étriers de frein des prochaines Chiron produites seront fabriqués avec du titane sur une imprimante 3D.
Texte : Steve Jolibois / Photos / Vidéo : Bugatti presse.
Non, vous ne rêvez pas. Le laboratoire technologique de la marque de luxe française se démarque en fabriquant les étriers de frein des futurs Chiron à partir d’une imprimante 3D, une première dans la construction automobile. Alors évidement, n’imaginez pas que l’impression se fait via du plastique fondu… Chez Bugatti on imprime avec du titane ! Un matériau bien plus noble et résistant. C’est à ce jour le plus grand composant fonctionnel en titane au monde fabriqué par un procédé d’impression 3D : 41 cm de long, 21 cm de large et 13,6 cm de haut.
En règle générale le titane s’utilise comme alliage de formule Ti6AI4V dans l’industrie aéronautique et aérospatiale pour la réalisation de composants soumis à de très fortes sollicitations mécaniques (suspensions de trains d’atterrissage, ailes d’avion, pièces de moteurs d’avion ou de fusée). Il dispose d’un avantage non négligeable par rapport à l’aluminium, avec une résistance à la traction de 1 250 N/mm2. Si cela ne vous dit rien, sachez que cet alliage peut être soumis à une traction légèrement supérieure à 125 kg par millimètre carré sans rupture. Son avantage réside aussi par sa légèreté. Pour preuve, les futurs étriers en titane pèsent 2,9 kg contre 4,9 kg pour un étrier en aluminium. Un gain de plus de 40 % en poids et un avantage au niveau des masses non suspendues.
Mais l’utilisation du titane ne présente pas que des avantages, surtout dans le domaine de la mise en œuvre. En effet, sa résistance extrême rend son usinage difficile et ne permet de fraiser ou de forger une pièce à partir d’un seul bloc. C’est donc tout naturellement que l’impression 3D est bénéfique à la réalisation des pièces spécifiques. Cette solution d’impression 3D a été réalisée au Laser Zentrum Nord, à Hambourg, qui a été intégré en début d’année à la prestigieuse Fraunhofer-Gesellschaft, un institut allemand spécialisé dans la recherche en sciences appliquées.
Le temps de développement d’un étrier de frein en titane à imprimer en 3D a été relativement court. Depuis le projet initial, jusqu’au premier modèle imprimé, trois mois se sont écoulés. Bugatti a transmis au Laser Zentrum Nord les données pour le concept de base : simulations de résistance, de rigidité et conception. Le centre a alors réalisé la simulation du procédé, la conception des structures de support, l’impression laser proprement dite et le traitement thermique du composant. Pour finir, Bugatti s’est ensuite chargé des opérations de finition.
L’imprimante 3D du Laser Zentrum Nord (la plus grande installation au monde adaptée au titane) dispose de quatre lasers d’une puissance unitaire de 400 W. Ainsi dotée, il lui faut 45 heures pour imprimer un étrier de frein avec le procédé suivant : l’imprimante dépose de la poudre de titane par couche. À chaque couche, les lasers interviennent pour faire fondre la poudre de titane en fonction de la forme souhaitée de l’étrier de frein. Le matériau est refroidit instantanément et l’étrier de frein prend forme. Un étrier de frein nécessite 2 213 couches au total. Une fois la dernière couche achevée, la poudre de titane non fondue est retirée, nettoyée et stockée, en vue de sa réutilisation. Après cela, l’étrier de frein subi un traitement thermique stabilisant qui lui donne sa résistance finale. Pour ce faire, il est passé dans au four (durant 10 heures) à des températures variant de 700 à 1000 °C afin d’éliminer les contraintes résiduelles et garantir la stabilité dimensionnelle du composant. L’étape suivante consiste à polir les surfaces à l’aide d’un procédé mécanique et physico-chimique combiné. Ce procédé augmente la résistance à la fatigue et, par conséquent, la durabilité à long terme du composant une fois installé sur le véhicule. Pour finir, les contours de toutes les surfaces fonctionnelles (chambres de pistons, filetages) sont usinés. Cette opération qui nécessite encore 11 heures de travail est réalisée par une fraiseuse 5 axes.
Les premiers essais de production en série débuteront au premier semestre de cette année, sans date précise. Les temps de production se réduiront ensuite progressivement, notamment lors de la phase de post-traitement, promet un ingénieur.
Comme l’indique *Frank Götzke, responsable des Nouvelles technologies au sein du département Développement technique de Bugatti Automobiles S.A.S : « Le développeur automobile n’a jamais le sentiment de la mission accomplie, c’est encore plus vrai pour nous, chez Bugatti. Nous ne cessons de réfléchir à la manière d’améliorer nos modèles actuels avec de nouveaux matériaux et de nouveaux procédés et d’imaginer à quoi pourraient ressembler les futurs concepts techniques des véhicules de notre marque. Les caractéristiques de puissance et de performance étant souvent proches des limites physiques, les exigences sont particulièrement élevées. C’est pourquoi Bugatti a toujours au moins une longueur d’avance sur les autres constructeurs en matière de développement de solutions techniques. Le Laser Zentrum Nord est l’une des nombreuses institutions scientifiques avec lesquelles nous avons établi une solide coopération au fil des ans. Du fait de ses innombrables projets déployés notamment dans l’industrie aéronautique, ce centre dispose d’un vaste savoir-faire dans le domaine du traitement du titane ainsi que de technologies éprouvées. Ces dernières années, les chercheurs de Hambourg ont obtenu de nombreux prix nationaux et internationaux de renom pour leurs travaux avec l’industrie. Tenir entre les mains notre premier étrier de frein en titane imprimé en 3D fut un moment très émouvant pour nos équipes. En termes de volume, c’est le plus grand composant fonctionnel en titane au monde produit par fabrication additive. Lorsqu’on le soulève, on est surpris par sa légèreté malgré sa taille imposante. C’est un composant à la fois très impressionnant d’un point de vue technique et merveilleusement esthétique. Bugatti est leader du développement de l’impression 3D au sein du groupe Volkswagen. Chacun peut et doit bénéficier de nos projets. C’est aussi la mission de Bugatti en tant que laboratoire du groupe pour les hautes technologies appliquées. L’étrier de frein en titane imprimé en 3D n’est qu’un exemple du travail de recherche et développement actuel de Bugatti. Nous avons non seulement développé le plus grand composant en titane produit par fabrication additive, mais aussi le plus long composant au monde en aluminium jamais imprimé en 3D d’une seule pièce », explique Frank Götzke en sortant fièrement de l’armoire une platine d’essuie-glace de 63 cm de long. « Avec ses 0,4 kg, elle ne pèse que la moitié du poids d’une platine en aluminium moulée sous pression classique, et ce avec la même rigidité. Mais c’est une autre histoire. »
L’avis de Testanddriving : Si Bugatti réalise une prouesse technique avec l’impression 3D, on espère que ce procédé est sûr, car la Bugatti Chiron utilise les freins les plus puissants au monde. Actuellement en alliage d’aluminium haute résistance, ses étriers sont forgés à partir d’un seul bloc. Ils comportent huit pistons en titane sur les étriers avant et six sur les étriers arrière. Ils pincent des disques de 420 et 400 mm de diamètre qui permettent de passer de 100 à 0 km/h en 31 mètres et de 400 à 0 km/h en 9,36 s pour une distance de 491 m. Un conseil, si un jour vous avez la chance d’apercevoir une Chiron sur la route, gardez vos distance sous peine d’être projeter dans le pare choc arrière en cas de freinage brutal…
*Frank Götzke fait partie du groupe Volkswagen depuis plus de 22 ans. Il travaille chez Bugatti depuis 2001 et a joué un rôle déterminant dans le développement de la Veyron en tant que responsable Développement châssis, puis dans le développement de la Chiron1 à son poste actuel.

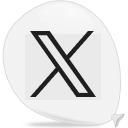




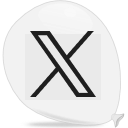


